|
Individual participants
|
European Partners |
CIMNE
|
The International Centre for Numerical Methods in Engineering (CIMNE, http://www.cimne.com/) is a research organization in Barcelona, Spain. CIMNE was created in 1987 as a Consortium between the Catalan Government (Generalitat de Catalunya) and the Technical University of Catalonia (UPC – Universitat Politècnica de Catalunya). CIMNE is an autonomous RTD centre focusing in promoting and fostering advances in the development and application of numerical methods and computational techniques for the solution of engineering problems in an international context.
CIMNE employs some 180 scientists and engineers from different technical fields and nationalities specialised in the development and of numerical methods to a wide class of engineering problems. The research activities of CIMNE cover the development of innovative constitutive models for composite materials and structures, new numerical methods for non linear analysis and safety studies of structures, shape optimization in structural and fluid dynamic problems, computational fluid dynamics studies for both external and internal flow problems and numerical simulation of material deformation and forming processes for the manufacturing industry, mesh generation and visualization interfaces, casting and thermal process, stochastic optimization as well as program parallelization and distributed (grid) computing techniques.
In the last twenty years CIMNE has taken part in over 450 RTD projects with over 200 companies and organizations. Some 110 of these projects have received EC support through FP3-7 programmes. CIMNE has been the coordinator of some 30 EC funded projects (including a cluster of projects in the FP5 IST programme). The outcome of the research is recorded in over 900 scientific publications, technical reports and educational software codes published by CIMNE. CIMNE has also successfully organized some 200 courses and seminars and around 60 international conferences. CIMNE has also specialized in the development of decision support systems integrating Artificial Intelligence models based on the Monte Carlo method, Neural Networks and IT tools such as wireless sensor networks and user friendly interfaces for finite element based simulation software. CIMNE received one of the 2002 IST Awards for a new software product named GiD [GiD 2003] for pre-processing analysis data and the visualization of numerical results from engineering computations (see www.gidhome.com). Also, in 2003 CIMNE received the City of Barcelona Award in Technological Research for the development of GID system “an innovative and easy graphic interface for modelization and visualization of numerical simulations results”.
Specific contribution to MARS Project
CIMNE contribution has three components.
The first one is devoted to the management of the project. CIMNE will be in charge of administrative management and Sheffield University will be in charge of technical management. We will contribute to WP1, then.
The second contribution is on WP3, mainly on tasks 3.1 amd 3.2. CIMNE will provide a code that has been developed by Professor Codina and his collaborators. It uses a method based on the numerical approximation of the sub-grid scales, which is an alternative to the more classical DNS or LES approaches for the numerical analysis. This code was used for the full analysis of the air flow around the GRANTECAN (the big telescope in Canary Islands recently inaugurated), and has been also used in the context of the F& project ELT-DS, also devoted to the aerodynamic analysis around telescope enclosures The complete analysis of these complex geometrical configurations requires 5-6 millions of elements and is performed on a workstation. A parallel version of the code is under development. The code is that it has been developed for incompressible flows. This code is also going to be used in the context of the VALIANT (VALidation and Improvement of Airframe Noise prediction Tools) FP7 project.
The final contribution is in WP4, mainly in task 4.2 devoted to Design optimization. CIMNE will provide its knowledge and expertise on optimization to facilitate seeking the best design of flow control devices. Optimization codes in use in CIMNE projects will be accessible for project use; Hybrid Nash Games, Multi-objective Evolutionary algorithms will be provided to the consortium.
|
Sheffield University
|
The University of Sheffield, which celebrated its centenary in 2005, is one of the UK’s leading research-led universities, with an international reputation for excellence in both teaching and research. In constantly developing the quality and diversity of its research across a wide range of subjects, the University has appointed many outstanding academics to its multidisciplinary research groups.
The Department of Mechanical Engineering at the University of Sheffield is one of the largest and most respected in the UK since its foundation in 1905, consistently achieving high ratings for teaching quality and research. It is internationally renowned for high quality research. The expertise of our staff covers a wide range of specialist areas and our mission is to carry out research for fundamental science through to practical industrial applications. Mechanical Engineering has received an outstanding result in the latest Research Assessment Exercise (RAE). The Higher Education Funding Council for England (HEFCE) has independently assessed research carried out by staff in every university department in the country. The quality of our research outputs, the research environment, research income, professional esteem, and PhD students are all rated and compared with our peers. Our profile is as 30% 4*, 45% 3*, 20% 2*, 5% 1*. This is an exceptionally good result and places us second in the country for Mechanical Engineering.
The Aerodynamics and Thermofluids group's research activities cover aerodynamics, combustion, turbulence and bio-fluids using both computational (CFD) and experimental tools. Major facilities include two recently refurbished low speed wind tunnels and a local parallel computing cluster. These facilities provide the group with the equipment for applied and fundamental fluid mechanic research and experiment-CFD side-by-side research for mutual validation and basic understanding. On-going research projects include: aerodynamic optimisation of blended wing body aircraft; shock control for aircraft drag reduction; flow control for separation control; multidisciplinary design and optimisation; aero-engine fuel emission control; synthetic jets for stall control; measurement and analysis of fluid flow in fuel cell systems; particle flow in human airway; simulation tools for micro-fluidic gases; fractal and wavelet analysis of turbulence and experiments; and real-time simulation of aircraft/vortex interaction.
Specific contribution to MARS Project
As technical co-ordinator of the overall project, Sheffield University will actively participate on WP1. Its primary research contribution will be to WP3 on the numerical simulation of flow control with its own simulation tools and facilities. It will also contribute in WP4 taking care of the core team which will evaluate the results from previous WP2 and 3. Details of its contribution are described in the work packages.
|
AIRBUS
|
Airbus consists of four national entities in France, Germany, UK and Spain. The history of Airbus has been one of the great industrial success stories of the last 30 years. 2003 was a landmark year for Airbus, the year in which it became Number One. 2004 was another key year for AIRBUS during which the aircraft manufacturer kept his position of n°1, concerning orders and deliveries.
Airbus has delivered 320 aircrafts in 2004. These deliveries represent 53 percent of the year’s total deliveries of more than 100 seats aircrafts, corresponding to a turnover of € 20 billion. In 2004, Airbus achieved 370 new firm orders representing USD 34 billion and 57 % of the market in numbers.
These results reflect the progressive leadership of Airbus in all market segments of this highly competitive market, in which the company today offers a complete product range – from 100 to 555 seats -, which is clearly becoming the reference. Airbus proposes a highly competitive as well as the most modern and complete product range of the industry:
Single aisle medium range aircraft: A318, A319, A320 and A321 (107,124,150 and 185 seats), Medium to long range wide body aircraft: A310 and A300-600 (220 to 266 seats), Very long range wide body aircraft: A340 (240 to 380 seats) and A330 (253 to 295). AIRBUS announced in December, 2004 the commercial launch of a new model derived from the A330 series; the A350. The A380 model (555 seats) first flight is scheduled beginning of 2005, and the first delivery in 2008.
AI-E is a private aeronautic company recently created in Spain as part of EADS group. The staff of AI-E originates from EADS CASA, the major Spanish large-scale aeronautical and aerospace industry with a total of 8000 employees and facilities located in Madrid, Sevilla and Cádiz. Since 1923, the company has been engaged in the development (design, manufacture and marketing) of aircraft in the field of both military and civil airplanes, being latest designed aircraft C-212 in several versions (civil and military), C-101 (military trainer aircraft), CN-235 and C-295 (military transport aircraft).
Besides this national activities AI-E is a partner through EADS CASA in various European programmes and organisations, the most important being EF-2000 Typhoon in addition to Airbus Industry and Arianespace membership.
Background information and experience
AIRBUS has long-term experience and expertise in the specification, industrialization and application of numerical methods for aerodynamic aircraft design and data production including single discipline optimization (SDO), multidiscipline analysis (MDA) and multidisciplinary optimization (MDO).
Since early 2000’s advanced developments have been achieved by Airbus in setting-up multi-physics simulation in the field of fluid-structure coupling for aeroelastics, conjugate heat transfer for aerothermics in ventilation of compartments, simulation of icing shape accretion, aeroacoustics for the simulation of noise source and propagation.
All these simulation are made by considering fluid simulation with a specific emphasis put on accuracy for drag prediction and optimization technique based on adjoint Navier-Stokes method.
The ONERA flow solver elsA is currently the major CFD capability in production usage for solving Navier-Stokes equations on structured grids The DLR flow solver TAU (unstructured RANS code) associated with the ARA hybrid- unstructured mesh generator SOLAR are under deployment for complex geometry. For multidisciplinary simulation Airbus is integrating EADS-M backbone SimServer for advanced multi-disciplinary simulation.
Airbus has participated in many EU projects dealing with optimization and multidisciplinary simulation and optimisation: ECARP, MDO, PROMUVAL, AEROSHAPE, VIVACE.
The staff of AI-E has wide experience in aircraft aerodynamic and structural design and analysis. It has become specialist in the field of horizontal tail plane design and manufacturing. In that way it has developed the horizontal tail plane of the successive Airbus Industry aircraft up to today. AI-E is responsible, among other parts, of the horizontal tailplane and belly-fairing of the recently launched A380. This experience has been accomplished and maintained thanks to the considerable effort of continuous funding to the field of research and development carried out by the company.
On the numerical side, Airbus has a wide experience in the development of numerical methods, both structured and unstructured as well as on the multi-physics domain.
Specific contribution to MARS Project
AIRBUS will contribute in WP1, WP2, WP4 and WP5 as shown earlier. AIRBUS will act as end-user of the project. It will provide general perspective and specific industrial application point of view to the whole project, but mainly in the validation phase. AIRBUS will contribute to specification definition as well.
|
FOI
|
The Swedish Defence Research Agency, FOI, is an assignment-based authority under the Swedish Ministry of Defence. The organisation employs around 1000 people of whom around 800 are researchers. FOI holds unique and very advanced laboratory equipment and computing facilities. The research at FOI covers a broad range of military, civil, and dual-use topics within its six research divisions. The aeronautics activities of the Division of Defence & Security, Systems and Technology span the fields of aerodynamics, structures and materials, flight mechanics, control systems, navigation, acoustics and environmental aspects of aviation. FOI has gained extensive experience of EC Framework programs on aeronautics, as well as of other national and international projects.
The FOI Department of Aeronautics and Systems Technology has remarkable experience and expertise of R&D for fundamental aerodynamic research and aeronautics applications, with an emphasis on computational aerodynamics and turbulence modelling, in a wide range of applications of, among others, flow control, fluid-structure interaction (FSI), aero-acoustics, propulsion, aerodynamic optimization, smart material, structural fatigue and damage, structural vibration and signal analysis. For computational modelling and simulations of aerodynamic flows, FOI has developed a well-recognized in-house CFD package EDGE. This CFD solver has been used in numerous aerodynamic applications for flow control, FSI and aero-acoustic analysis. FOI has actively participated in a number of national and international projects in relation to CFD, turbulence modelling and their aeronautic applications, among others, many recent EU projects, including HiAer, FLOMANIA, NACRE, TELFONA, SUPERTRAC, DESider, HISAC, REMFI, ALEF and ATAAC. Based on previous experience and expertise in fundamental research and in industrial applications, FOI will make important contributions to the objective of the project.
Specific contribution to MARS Project
Together with other relevant and interesting partners, FOI will participate in WP 1 and WP 4. A major part of the proposed FOI work will be placed in WP3 , in which FOI will address the modelling and simulation methods for turbulent flows manipulated by flow-control devices to attain accurate and reliable numerical analysis.
At FOI, numerical analysis of different control devices has been performed in a number of previous project work, including micro-jets of different types and vortex generators. Currently, we are also working on flow separation control using plasma actuators, in which the effect of plasma actuators on the external flow is incorporated as a body force vector in the Navier-Stokes equations. The main tool to deploy will be numerical approaches
|
ALENIA
|
ALENIA AERONAUTICA, owned at 100% by Finmeccanica, designs and develops products for civil and military aviation. Through alliances or joint ventures, Alenia Aeronautica participates in the world's leading civil and military programmes, both independently and as risk-sharing partner.
Its commercial aviation activities include the assembly of complete fuselages and the production of fuselage sections and components for aero-structures. Alenia Aeronautica is also a primary manufacturer of regional aircraft. In the context of international co-operative programmes and consortia, it is a primary manufacturer of military aircraft, with activities including aircraft design, production, integration and marketing, along with the managing of flight tests and final assembly lines. Alenia Aeronautica boasts decades of experience. Its factories have built or overhauled over 12,000 of the main civil and military aircraft. The company was formed in 2001 from the aeronautical division of Finmeccanica, itself the heir to the experience of Aeritalia and Selenia. Alenia Aeronautica participates, also through alliances and joint ventures, in the leading international civil and military programmes.
In the military field, Alenia Aeronautica Has a 21% share in the Eurofighter Typhoon programme. It supplies on-board systems, the left wing and the rear fuselage. It is responsible for final assembly and flight-testing of aircraft ordered by the Italian Air Force. The first Eurofighter Typhoon was delivered to an Italian Air Force operational unit in March 2004; builds the C-27J tactical transport aircraft, through the equal share LMATTS joint venture with Lockheed Martin; developed the AMX subsonic attack aircraft and advanced trainer, together with Aermacchi and Embraer of Brazil; Participated in the Panavia consortium (with BAE Systems and EADS) with a 15% share of the Tornado programme.
In the commercial jet business, Alenia Aeronautica produces aero-structures for Boeing and Airbus, acting as both risk sharing partner and sub-contractor. It is present in the two leading programmes in this field, the A380 superjumbo and the future 7E7. It is a partner of Dassault Aviation in the production of the Falcon business jet family. In the field of special mission aircraft, it produces and markets the ATR42 MP maritime patrol aeroplane and is developing the ATR72 ASW. Through ATR Integrated, an equal joint venture with EADS, Alenia Aeronautica ranks among the main world's producers of regional aircraft with the ATR42/72 twin turboprop.
Background information and experience
Alenia Aeronautica has a large experience and expertise in the development and application of numerical tools for aircraft design in the fields of aerodynamics, fluid/structure interaction, multidisciplinary analysis and optimization. Since the early nineties, they participate to more than 25 European initiatives in the Flight Physics Technologies field.
Specific contribution to MARS Project
Main involvement of Alenia Aeronautica in the MARS project is in the specification of requirements on test cases and in the industrial assessment of selected flow control devices by extrapolation to real world applications.
|
DLR
|
The German Aerospace Center (DEUTSCHES ZENTRUM FÜR LUFT- UND RAUMFAHRT) is the national center for large-scale aero¬space research and the greatest research establishment for engineering sciences in Germany. DLR has considerable experiences in aerodynamic design, numerical and experimental simulation, testing in large facilities, and analysis methods.
Over the last 20 years numerical methods for complex aircraft configurations based on the solution of the Euler- and Navier-Stokes equations on structured and unstructured grids have been developed. The DLR flow solvers FLOWer and TAU are routinely used in the German aircraft industry and at several German universities. They are world wide recognized tools with excellent reputation. Currently DLR is developing its next generation flow solver based on adaptive higher-order Discontinuous Galerkin methods. The capabilities of DLR have been proven in many national and international projects including several CFD related EU projects.
In particular, DLR has a long lasting experience of technology transfer from fundamental research to industrial application. Strong links to universities have been established within the national projects MEGAFLOW and MEGADESIGN, guaranteeing a continuous flow of research results into the current code development, making the latest technology available to industrial application within short time. DLR assists a close cooperation with the German aeronautical industry, assuring rapid feedback on provided technologies and further industrial needs.
The Institute of Aerodynamics and Flow Technology of DLR, located in Braunschweig and Göttingen, has long years’ experience in the development and application of mobile image based measuring systems such as Pressure Sensitive Paint, Temperature Sensitive Paint, Particle Image Velocimetry, Density Measurement Methods, and Model Deformation Measurement Systems for aerodynamic investigations in large wind tunnels. These systems have been successfully applied in many low- and high-speed European wind tunnels in the last years (DNW: LLF, HST, TWG, LST, NWB, KKK together with ONERA in the B20 catapult facility and S2). Recently the section Experimental Methods, located in Göttingen, successfully performed the PIV tests in large wind tunnels for the EUROPIV, APIAN, EUROWAKE, WAVENC, C-WAKE, EUROLIFT 1 and 2, and EUROPIV 1 and 2 projects. PSP tests have been performed in collaboration with industry (AIRBUS Deutschland LSWT, Bremen; EADS, AERMACCHI) in transonic wind tunnels and in ETW. The TSP technique has been developed as powerful tool for transition detection in cryogenic flows (ETW). Most of the experimental work in large wind tunnel has been performed with the objective to provide experimental data for comparison with the results of numerical calculations. Thus, cooperation between experimentalists and CFD specialists has been a key element of our work in the past years.
Background information and experience
DLR is Germany´s national research center for aeronautics and space. Its extensive research and development work is integrated into national and international cooperative ventures. As Germany´s space agency, DLR has been given responsibility for the forward planning and the implementation of the German space program by the German federal government as well as for the international representation of German interests. Furthermore, Germany’s largest project-management agency is also part of DLR.
Approximately 6,500 people are employed in DLR´s 29 institutes and facilities at 13 locations in Germany: Berlin, Bonn, Braunschweig, Bremen, Cologne (headquarters), Göttingen, Hamburg, Lampoldshausen, Neustrelitz, Oberpfaffenhofen, Stuttgart, Trauen and Weilheim. DLR also operates offices in Brussels, Paris, and Washington, D.C.
DLR’s mission comprises the exploration of the Earth and the Solar System, research for protecting the environment, for environmentally-compatible technologies, and for promoting mobility, communication, and security. DLR’s research portfolio ranges in its key areas Aeronautics, Space, Transportation und Energy from basic research to innovative applications and products of tomorrow. In that way DLR contributes the scientific and technical know-how that it has gained to enhancing Germany’s industrial and technological reputation. DLR operates large-scale research facilities for DLR’s own projects and as a service provider for its clients and partners. It also promotes the next generation of scientists, provides competent advisory services to government, and is a driving force in the local regions of its field centers.
Specific contribution to MARS Project
DLR will contribute on WP2 with its knowledge of measurement techniques, and in WP4 to ensure a good understanding of these measurements.
|
Université de Poitiers
|
Established in 1431, the University of Poitiers is the second oldest university in France and counts François Rabelais, René Descartes, and Francis Bacon amongst its former students. Highly regarded within France, the University of Poitiers provides 24,000 students a full range of top quality courses in Science, Liberal Arts, Pharmacy and Medicine, Engineering, Law, Economics, and Management. The University is developing high standard research in numerous fields thanks to its renowned research facilities. The university is associated with CNRS for 20 research laboratories among a total of 45.The research potential in human term is of 870 assistant professors and professors, and 100 researchers assigned by CNRS.
The LEA (Laboratoire d’Etudes Aérodynamiques, Université de Poitiers, CNRS UMR6609) focuses on fluid mechanics, and in particular on the study of steady, unsteady and turbulent flows, both compressible and incompressible. The laboratory research activities are supported by high-performance experimental facilities and a wide range of analysis and measurement techniques.
Background information and experience
The ‘TAMCO’ group (Turbulence, Analyse, Modélisation, contrôle) at LEA Poitiers is particularly engaged in turbulent measurements and conceptual approaches for airflow control, especially in free shear flows. As far as turbulence is concerned, the group is specialized in analyzing different contributions to Reynolds stresses, including multiple decomposition concepts, interactions between different scales, stochastic descriptions, etc. It is then proposed to post-process the experimental data in view of Reynolds stress behaviour.
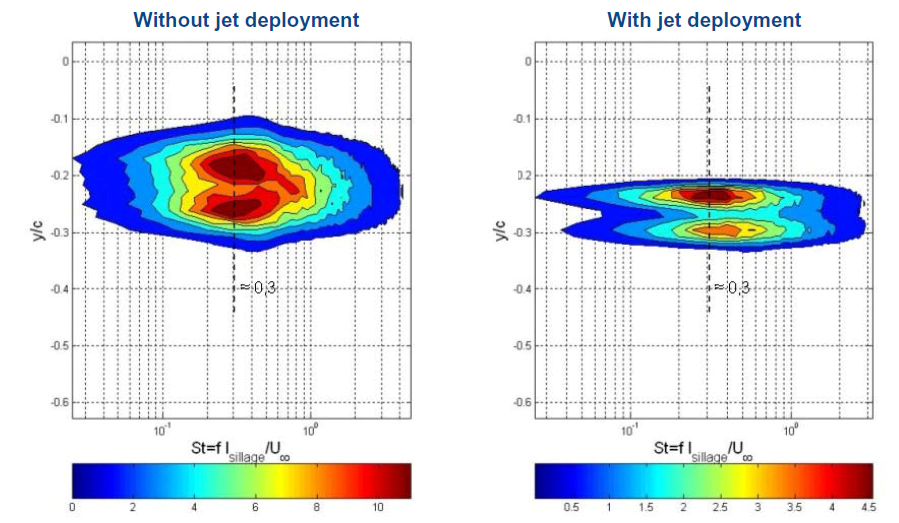
Frequency signature in the wake of a NACA 0015 model controlled by FVG.
 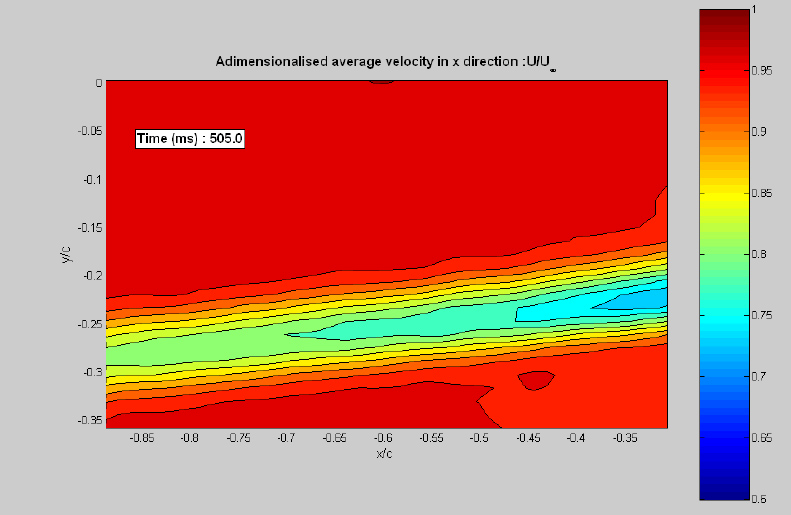
Natural and controlled wake (FVG) of a trailing edge separation over NACA 0015 airfoil model
The ‘EFD’ (Electro-Fluido-Dynamic) group composes one research component of the LEA (11 permanent researchers, plus 10 doctoral and post-doctoral positions). This group has a strong background in plasma discharge and flow control by plasma actuators. Initial control studies using plasma actuators have been realized since 1999, before the current keen interest on this topic. This has positioned the LEA as a European pioneer. Currently composed of specialists in electrical engineering and fluid dynamics, the competence of the EFD group covers all the physical domains involved.
One part of the current activities relates to the actuator itself. The momentum transfer produced by a surface discharge is experimentally analyzed by a spatio-temporal approach for different geometric and electrical designs to optimize the electro-mechanical effectiveness of such actuators. Our recent investigations have demonstrated the capabilities of plasma actuators for multi-frequencies excitation. This opens new flow control strategies. Our group is also involved in the development of innovative actuators designed for large scale flow applications. These actuators are implemented in open and closed-loop control approach to delay the separation over airfoil, to improve the mixing in the wake of axisymmetric jet, to minimize the drag of bluff body and more generally to manipulate the vortex dynamic dominating in the studied flow.
At LEA, the group involved in flow control by plasma has a strong experience of flow manipulation for various aerodynamics configurations. Usually, typical DBD was used to control separated airflow, to modify the near and far field regions of axisymmetric airjet, this by open and closed loop approaches. The group benefits from the experience developed at LEA in laser diagnostics, unsteady wall measurements, time-resolved and turbulent flow analysis. Based on the well-known competence of the group, the impact of typical DBD (i.e., driven by a AC frequency of about a few kHz) will be investigated for single and multi-DBDs configurations. In particular, modifications of the Reynolds stress tensor by using linear and nonlinear forcing will be investigated. Indeed, as recently demonstrated, the low time-response of plasma actuators can be used to produce small amplitude fluctuations at single, dual and multi-frequencies. This may enhance or cancel nonlinear interactions developing in free shear layer. The present project also includes the development of an innovative DBD actuator related to nanosecond pulsed discharge. Strong changes in the turbulent flow field are expected.
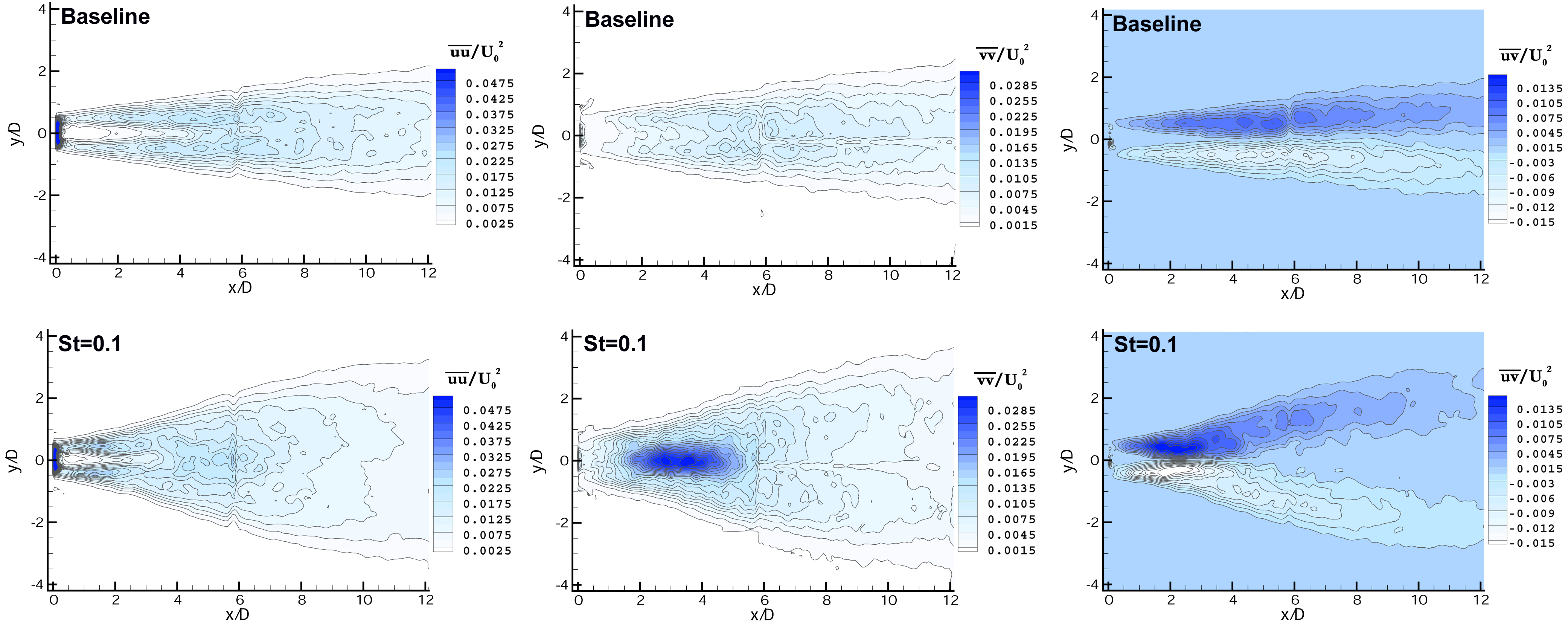
Reynolds stress component in the wake of an axisymmetric jet controlled by DBD plasma actuator (large field reconstructed by three CCD PIV)
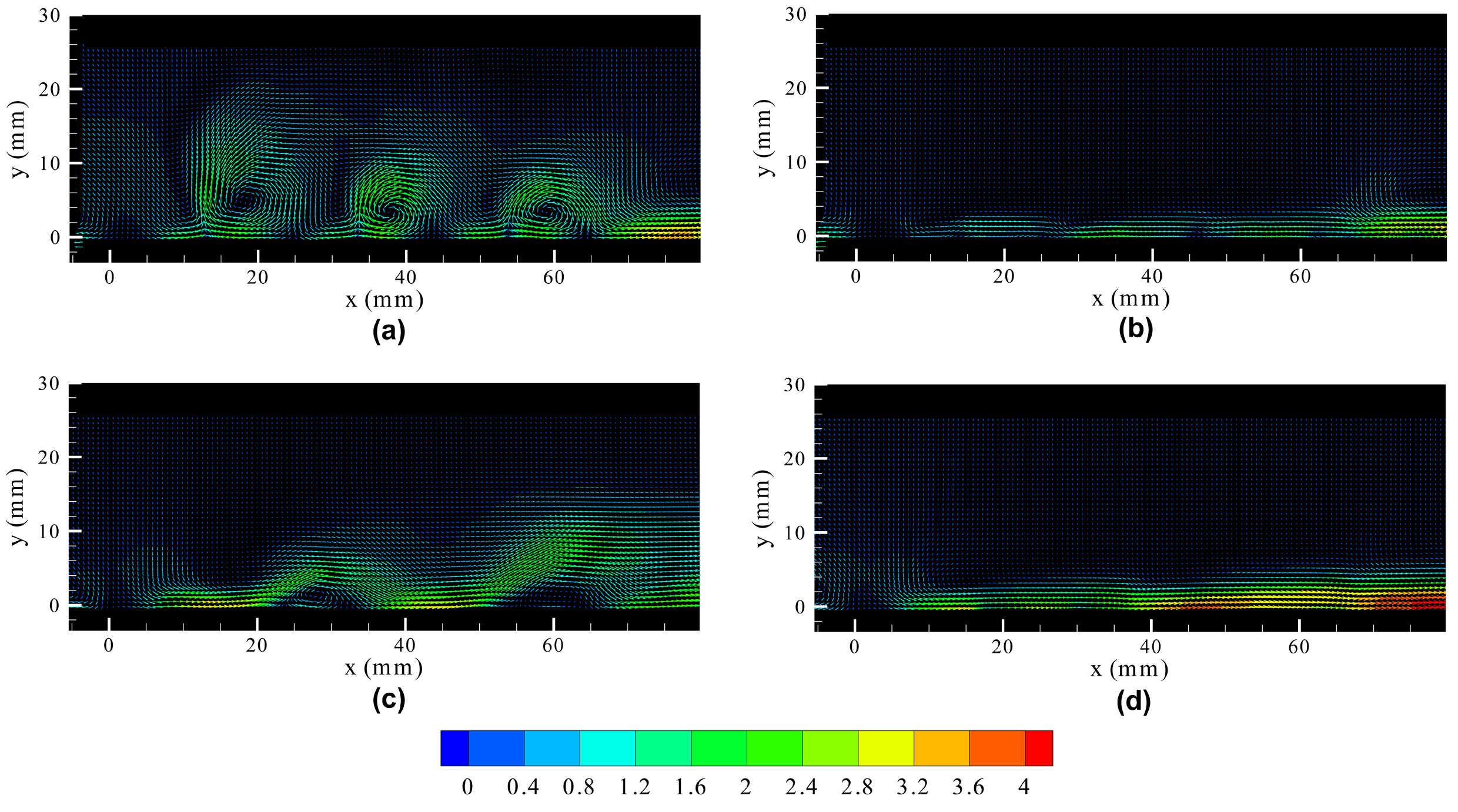
Induced airflow by multi-DBDs with typical electrodes (left caption) and innovative three-electrode design (right caption). Scale is in m/s, TR-PIV acquisition.
Specific contribution to MARS Project
The University of Poitiers is involved WP2, focusing on experimental tests of flow control devices.
|
DASSAULT Aviation
|
Dassault Aviation is one of the major players in the global aviation industry, with a presence in more than 70 countries across the 5 continents, whose varied activities cover several areas of high technology. With about 8300 people, the Dassault Aviation's primary vocation is the design, development, production, sale and maintenance of aircraft.
In 2008, the FALCON turnover represented 62 % of the overall turnover.
In total, Dassault Aviation has sold more than 2000 FALCON aircraft of all types over the last 40 years. 90 % of them have gone for export (about 2/3 of which to the USA). They represent 50 % of the top-of-the-range world market. Today, the Dassault Aviation FALCON family in production comprises the FALCON 900 and FALCON 2000 with various versions such as the EX (Extended range), EASy (Enhanced Avionics System), DX and LX version. It also comprises the FALCON 7X, with a new innovative wing design and a fly-by-wire flight system. The FALCON 7X has been certified in April 2007, both by EASA and FAA. Deliveries have started a few weeks later.
One FALCON takes-off or lands each minute around the world.
The FALCON family contributes enormously both to the reputation of European executive aircraft and to the European economy. It contributes to maintaining the industrial base of a European high technology sector. FALCON have been developed and produced in European co-operation with partners from Belgium (SABCA), Italy (ALENIA - PIAGGIO) and Greece (Hellenic Aircraft Industries). Many European partners have been involved in the development of the new FALCON 7X business jet. The main ones are : Spain (CASA), Netherlands (STORK), Belgium (SONACA).
Among the numerous FALCON types, Dassault Aviation has developed multirole versions, such as maritime surveillance versions used by the French and the US Coastguards, to ensure their coastline security and integrity.
The Research and Development employs nearly one quarter of the company's workforce. Fundamental and pre-competitive research is usually carried out in close co-operation with universities, research institutes and other industrial partners via a wide international network.
Background information and experience
Physical flow phenomena such as turbulent boundary layer separation strongly influence wing performance. Classical wing design through shape optimisation enables separation to be controlled to a certain extent but seems nowadays only to offer a limited potential for further improvements at given design conditions. Active flow control technologies, when carefully applied and developed, may open the door to significant progress. These technologies are clearly multi-disciplinary and imply not only a good knowledge of the aerodynamic improvement, but also a strict analysis of their impact on the wing structure and systems in order to globally identify the related benefits and penalties.
Turbulence and separation control is of highest interest for both low and high-speed issues. For instance, at low speed significant improvement of the high-lift performance has been evidenced by means of sub-boundary layer mechanical or pneumatic vortex generators resulting in reduced aircraft noise. Another important trade-off, which could be possible thanks to active flow control, is the simplification (in terms of less complex system, and thus lower cost and lower weight) of the high lift devices. At high speed one potential benefit of active control would be the postponement of buffet limits to higher lift coefficients or higher speeds. Pitch-up limits, inherent to highly swept transonic wings, could be also addressed by postponing shock boundary layer separation. Furthermore microsystems technology (MEMS) for actuators/sensors, which is under development worldwide, promises remarkable advances in active flow control. Nevertheless, further specific effort must be devoted to the technology of integrated actuators able to deliver higher velocities than existing ones in a pulsating mode.
Flow control is one of important concerns within the Advanced Aerodynamic Department at DASSAULT-AVIATION, and has been studied for more than ten years, through national R&T projects in collaboration with research centres and universities, as well as EC projects like EUROSHOCK, AEROMEMS , EUROLIFT2, and AVERT. Dassault Aviation was also leading the Technical Area 3 (Flow Separation Control Technologies) within the recent KATnet2 project.
Concerning CFD code Dassault Aviation will use within the MARS Project its own in-house unstructured Navier-Stokes solver Aether which includes many turbulent models (K-eps SST, K-KL , K-KL EARSM ,..) in a RANS mode and in URANS mode, as well as DES capabilty for unsteady computations.
Specific contribution to MARS Project
DASSAULT AVIATION will contribute to WP4 in contributing to the review, the understanding and the synthesis of work performed in WP2 and WP3, and identifying one or two devices for effective flow control in the aircraft environment. DASSAULT AVIATION will also contribute in WP5 related to industrial demonstration and evaluation of flow control techniques issued from WP2,3 and 4.
|
NUMECA INTERNATIONAL
|
NUMECA Int. is a Belgian SME (http://www.numeca.com), with headquarters located in Brussels, active in the development and marketing of advanced Computational Fluid Dynamics (CFD) software, grid generation and scientific visualization. Founded as a result of research activities carried out in the field of CFD at the Department of Fluid Mechanics of the Vrije Universiteit Brussel (VUB), NUMECA has been growing steadily and has progressively gained worldwide recognition. Presently, NUMECA has over 50 engineers and PhD scientists at its headquarters in Brussels, and another 25-30 active in its worldwide network. The NUMECA software allows simulation, design and optimization of fluid flow and heat transfer and worldwide manufacturers trust NUMECA for the superior performance, reliability and ease-of-use of its software and for its professional services.
NUMECA is today an innovative provider of computational fluid dynamics (CFD) software and consulting services oriented for a large part towards the area of aeronautics and propulsion. NUMECA is indeed heavily focusing its CFD software products FINETM/Turbo, the automatic grid generator AutogridTM and FINETM/Design3D, towards the aerospace, propulsion and energy markets with a significant percentage of NUMECA customers being connected to the aerospace sector. FINE™/Design3D is a dedicated and fully integrated software environment for turbomachinery blade shape optimisation, developed by NUMECA and several industrial partners, largely in use with several turbomachinery and engine manufacturers. NUMECA has a broad experience with EU projects and is currently involved in several FP7 projects, such as ERICKA (optimisation of cooled turbine blade components), ATAAC (on advanced turbulence models for aeronautics), FFAST (on Reduced Order Modelling techniques for aeroelastic simulations), VALIANT (on broadband aircraft noise analysis). NUMECA was also involved in several recently terminated projects, such as DESIDER (DES methods for aeronautics), UFAST (on shock boundary layer interactions). In addition, NUMECA acted as coordinator of the ADCOMB-CFD Marie-Curie Project, related to combustion modelling, and is presently coordinator of a follow-on project COMBINA, oriented at premixed combustion modeling.
NUMECA is coordinator of the FP6 NODESIM-CFD project (http://www.nodesim.eu) oriented at the incorporation of uncertainties in CFD simulations, by non-deterministic methodologies. NUMECA was also heavily involved in an earlier EU funded network QNET-CFD dealing with best practice guidelines for CFD, which was coordinated by Prof. Ch. Hirsch, as Head of the Department of Fluid mechanics of the VUB.
Specific contribution to MARS Project
NUMECA plan to contribute to the simulation tasks of the project test cases, WP3, and eventually to the optimisation tasks, as well as to WP4 and WP5.
|
Manchester University
|
The University of Manchester was created by bringing together The Victoria University of Manchester (VUM) and UMIST, two of Britain's most distinguished universities, to create a powerful new force in British Higher Education. Manchester has a long tradition of excellence in Higher Education. UMIST can trace its roots back to 1824 and the formation of the Manchester Mechanics' Institute, whilst The Victoria University of Manchester was founded as Owen's College in 1851. After 100 years of working together, these two institutions were formally combined to form a single university in 1 October 2004. Twenty-three Nobel Prize winners have studied here: Rutherford began his work here on splitting the atom, and the world's first computer also came into being at The Victoria University of Manchester. In the field of Fluid Mechanics, Osborne Reynolds, FRS, the first professor of engineering in England, spent his whole professional life at Manchester, during which (among his astonishingly wide-ranging contributions) he shaped the direction of turbulence research for the century which followed. The School of Mechanical Aerospace and Civil Engineering was created from UMIST's Department of Mechanical, Aerospace & Manufacturing, the Department of Civil & Construction Engineering and VUM’s School of Engineering; all three of the existing departments were awarded category 5 rating in the 2001 RAE. The University enjoys close collaborations with industry and other research organizations, both nationally and internationally.
The University of Manchester Aerospace Research Institute (UMARI) plays a vital role in positioning the University of Manchester at the forefront of international aerospace research.
The North West of England is the most important aerospace region within the UK and, being based in Manchester, the heart of the North West, we are keen to exploit this to become a world force in aerospace research and innovation. The Aerospace Research Institute operates on an interdisciplinary basis right across the University, bringing together every aspect of aerospace research which is innovative and united.
The Aerospace Research Institute also aims to:
- Achieve a doubling of our aerospace research portfolio to become one of the top three Universities for aerospace research
- Expand the research base by fully exploiting world class technologies and skills within the University not presently associated with aerospace
- Recruit virtuoso scholars and researchers
- Make the University of Manchester the University of choice as an aerospace collaborator in new projects and initiatives within Europe, nationally and regionally by establishing a portfolio of major aerospace related initiatives
- Develop the skills and proficiency of graduates and post graduates in aerospace
- Enable the University to access outstanding students from abroad.
- Collaborate, as appropriate, with other universities in the North West to advance the interests of the region, building on the collaborative success of the North West Composites Centre, North West Laser Engineering Consortium, NATEC and the North West Aerospace Alliance.
Specific contribution to MARS Project
The University of Manchester has a long experience and expertise on the development and application of a wide range of flow control actuators for both low and high speed applications. It has developed and studied extensively synthetic jets, flexible and oscillating surfaces, micro-jets, grooves, vortex generators, plasma actuators (DBD, Spark-Jets, Corona Discharge, Sliding Discharge, arc jets) etc. UNIMAN is also a world leader in the development of advanced flow diagnostics and instrumentation techniques such PSP, high speed PIV, liquid crystals, skin friction probes etc. In the present proposal, it will contribute in WP2 and WP4. In WP2, UNIMAN will conduct detailed experiments on a step geometry and a NACA0015 aerofoil using its subsonic wind tunnel facilities together with the associated instrumentation. It will demonstrate the ability to measure the contribution of the periodic flow to the global Reynolds stresses using its existing flow diagnostic techniques. It will study the basic flow physics, and turbulence characteristics and receptivity of the separated flow. It will define and characterise synthetic jet actuators and elastic/flexible surfaces, will evaluate their effectiveness to control the unsteady components, and then will assess the effects of apparent stress on Reynolds stress. It will also measure the effects of Reynolds stress on stream wise skin fiction and separation. In WP4, UNIMAN will contribute to the synthesis from experimental and computational data collected in WP2 and WP3. More specifically, it will analyse the data collected to improve the understanding of flow control on Reynolds stress, and together with the other partners will assess and compare the control effectiveness of the devices tested on oscillating separated flow, prevention of separation or drag reduction.
|
INRIA
|
INRIA (National Institute for Research in Computer Science and Control) is a French public sector scientific and technological institute with 2100 employees, operating under the dual authority of the Ministry of Research and the Ministry of Industry. The research carried out at INRIA brings together experts from the fields of computer science and applied mathematics covering the following areas: Networks and Systems; Software Engineering and Symbolic Computing; Man-Machine Interaction; Image Processing, Data Management, Knowledge Systems; Simulation and Optimization of Complex Systems.
Opale Project-Team has several objectives : analyze mathematically single or multi-disciplinary coupled systems of partial differential equations arising from physics or engineering in view of their optimization or control ( geometrical optimization); contruct and experiment efficient numerical approximation methods (coupling algorithms, model reduction) and optimization algorithms (gradient-based and/or evolutionary algorithms, game theory); develop software platforms for the distributed parallel computation of the related discrete systems.
INRIA, the national institute for research in computer science and control, operating under the joint authority of the Ministries of Research and of Industry, is dedicated to fundamental and applied research in information and communication science and technology (ICST).
The Institute also plays a major role in technology transfer by fostering training through research, diffusion of scientific and technical information, development, as well as providing expert advice and participating in international programs. By playing a leading role in the scientific community in the field and being in close contact with industry, INRIA is a major participant in the development of ICST in France.
Throughout its six research units located in seven major regions, INRIA has a workforce of 3,200, 2,400 of whom are scientists from INRIA or from INRIA’s partner organizations such as CNRS (the French National Center for Scientific Research), universities and leading engineering schools. They work in 120 joint research projects-teams. Many INRIA researchers are also professors who supervise around 800 doctoral students, their theses work contributing to INRIA research projects.
INRIA has an annual budget of 125 million euros, one quarter of which comes from its own research contracts and development products.
The Institute’s strategy closely combines scientific excellence with technology transfer. INRIA’s chief goal for 2003-2007 is to achieve major scientific and technological breakthroughs in the following seven priority grand challenges:
- Designing and mastering the future network infrastructures and communication services platforms
- Developing multimedia data and multimedia information processing
- Guaranteeing the reliability and security of software- intensive systems
- Coupling models and data to simulate and control complex systems
- Combining simulation, visualization and interaction
- Modelling living structures and mechanisms
- Fully integrating ICST into medical technology
INRIA develops many partnerships with industry and fosters technology transfer and entrepreneurship in the field of ICST - some eighty companies have been founded. Start-ups are supported in particular by INRIA-Transfert, a subsidiary of INRIA that promotes four startup funds in the field of information and communication technology.
INRIA is participating in such standardization committees as the IETF, ISO or the W3C of which INRIA was the European host from 1995 to 2002.
INRIA asserts its presence in the international research particularly in contributing to the development of the European Research Area through its implication in ERCIM (consortium of 18 European research institutions) and its participation to the 6th Framework Program. To foster the exchanges INRIA set up collaboration programs such as: “Associate Team Program” (26 Associate Teams in 11 countries), “internship” (around 80 foreign interns), develop an incentive strategy of training (31% foreign PhD’s students) and hosting (1000 foreign visitors from 70 countries) while participating to the INRIA recruitment policy of foreign researchers (30% of foreign tenured scientists in 2003 and 2004).
Background information and experience
INRIA (National Institute for Research in Computer Science and Control) is a French public sector scientific and technological institute under the responsibility of the Ministry for Research and the Ministry of Industry. INRIA employs over 1300 people including 1000 scientists, among which 340 tenure positions, 330 scholar and trainees, 180 researchers from public laboratories, 50 engineers from industry, 100 visiting researchers from abroad. The research carried out at INRIA is mainly concerned with software and control engineering. This research brings together experts from the fields of applied mathematics, control, signal processing and computer science within the frame work of 6 research programmes. Parallel Architectures, Databases Networks, Distributed Systems Symbolic Computing Programming, Software Engineering Artificial Intelligence, Cognitive Systems. Man-Machine Interaction Robotics, Image, Vision Signal Processing and Control, Computer-Integrated Manufacturing Scientific computing numerical analysis computer-aided engineering.
INRIA has a long experience of international cooperation and coordination responsible for the building of Modulef (300 installations/members), early contributing to build European structures as ERCIM, ERCOFTAC, ECCOMAS. Spatial CFD networks (Hypersonic database) and many CEC projects. The group OPALE gathers working on the design of efficient and accurate numerical methods for the simulation of complex compressible flows on unstructured meshes. INRIA has several years of experience in theoretical and experimental studies related to optimal control model problems and optimum design problems (industrial aerodynamics and electromagnetics) solved using Gas, among others. It has also several years expertise in building databases for CFD testcases (FLOWnet, INGEnet and PROMUVAL), as well as parallel, cluster and grid computing environments applied to CFD optimisation and aerostructure problems.
Specific contribution to MARS Project
INRIA will contribute in WP3 providing the implementation of models of flow control devices into an in-house flow solver. High-Performance Computing (HPC) facilities will be used systematically to reduce CPU costs. INRIA will also contribute on WP4.2; INRIA will conduct the automatic optimization of control devices by coupling the flow solver with optimization algorithms developed at INRIA.
|
EADS-IW
|
The EADS Innovation works is the transnational R&D centre for the EADS group. The missions of EADS IW are:
- As a global R&T partner, the EADS Corporate Research Centre enables superior return on R&T investment and regional presence through: an open and flexible organization; maximizing its innovation potential through a high degree of co-operation and integration with public and private research organizations; acquiring and promoting the best available knowledge.
- Assure added value by synergy of shared research inside EADS and by cooperation with research partner organisations (e.g. DLR, INTA, ONERA, Universities, Laboratories…).
- Maintain and develop innovation potential for long term technological competitiveness of EADS.
- Enable emerging technology integration in current and future EADS products.
- Support EADS technology strategy.
Some of the competitive advantages to products, processes and services of the EADS group are:
- Providing services in intellectual property and standardisation.
- Multidisciplinary know-how combining expertise and shared facilities.
- Developing new tools and methods for processes in design, testing, manufacturing, simulation and quality assurance.
- Accelerated transfer of results into products and services.
- Rapid reaction force for technical consultancey.
- Advanced expertise and skills.
Background information and experience
Composites Aerostructures
Metallic Aerostructures
Systems, Avionics, Equipment & Sub-systems
Flight Mechanics, Structural Dynamics
Integration, Design & Validation
Specific contribution to MARS Project
The Innovation Works office of EADS UK will participate in MARS. This office is the UK element of the transnational corporate research organisation EADS Innovation Works. EADS Innovation Works UK is a partner in ongoing research which seeks to develop reduced order streak prediction models that can be applied at high Reynolds numbers. The ultimate objective of this work is to be able to predict the drag reduction that arises from differing wall based flow control strategies for civil aircraft in cruise.
|
Chinese Partners |
AVIC-ARI
|
AVIC Aerodynamics Research Institute (AVIC ARI) was established in 2000 by merging former Harbin Aerodynamics Research Institute with Shenyang Aerodynamics Research Institute. AVIC ARI is governed by China Aviation Industry Corporation (AVIC) and has more than 700 employees. As the unique aerodynamic research institution in China aviation industry, AVIC ARI is mainly engaged in aeronautic aerodynamic fundamental research, aircraft aerodynamic configuration design, CFD technology research and application, wind tunnel test technology research, and special testing equipment design and manufacture.
Currently, there are seven facilities, including 0.6m×0.6m trisonic wind tunnel, 1.2m×1.2m trisonic wind tunnel, 1.5m×1.6m trisonic wind tunnel, F1.5m low speed wind tunnel, 0.64m×0.52m transonic wind tunnel, 3.5m×2.5m low speed wind tunnel, 4.5m×3.5m pressurized low speed wind tunnel. Furthermore, an 8m×6m low speed wind tunnel is under construction and its expected operation is in 2012.
Background information and experience
AVIC ARI has seven facilities covering low speed, transonic and supersonic regions. Every wind tunnel is equipped with advanced measurement equipments and has the ability of performing the conventional tests and special tests. There are many sophisticated test techniques in AVIC ARI especially for flow field measurement.
A lot of resources and efforts have been dedicated in recent years to research activities in complex and dynamic flow visualization and measurement, especially vortex diagnosis.
Moreover, AVIC ARI’s own codes have the abilities of numerical simulation based on RANS as well as DES&LES. Also, several optimization researches have been developed and applied in aircraft industry.
Brief Introduction of Flow Control Group in AVIC-ARI
- 25 employees: 10 for CFD & Optimization + 15 for Experiment
- CFD Codes: Structured Grid Solver, Unstructured Grid Solver
- 7 Wind tunnels: low speed, transonic(including continuous wind tunnels)
- Many Test Techniques: Force Measurement, Flow Field Measurement (PIV, PSP ect.)
- Synthetic Jet: design and optimization by CFD, validation by Exp. with SJ
- VG: Control of flow separation of inlet and civil transport by CFD and by Exp.
- Plasma: Plat with Plasma by CFD, Plat and airfoil by Exp.
Specific contribution to MARS Project
As the administrative coordinator of MARS project, AVIC ARI will contribute to the whole project, including WP1~5. Using our own simulation tools and facilities, AVIC ARI’s work will cover experimental researches, computational simulations, optimizations and demonstrations. The details of its contributions are described in specification of work packages.
|
NUAA
|
NUAA (Nanjing University of Aeronautics and Astronautics), established in 1952, is one of the key universities in China with the combined features of aeronautics, civil aviation and astronautics. NUAA consists of 10 colleges, and has set up as many as 50 research institutes and has very strong advantages in the research and application of basic science and the development of high technology. NUAA has developed "CK" series of super pilot less aircraft, AD series of super-light airplanes and other series of helicopters, and it has also made a lot of breakthroughs in many key projects concerning aeronautic and astronautic research and national defense programs.
The Research Institute of Aerodynamics in NUAA has large-scale facilities for both aerodynamic experiments and CFD, including 3m low speed wind tunnel, 0.6m high speed wind tunnel, 1.5m low speed unsteady wind tunnel, SGI work station and PC clusters with 128 CPU. The research activities are supported by NSFC, ministries and industry. Experience in development and application of measuring techniques, computational methods and design optimization will facilitate NUAA team in the international cooperation.
Background information and experience
Since 1980s flow control has been one of the most important topics in the Research Institute of Aerodynamics and some innovations has been achieved both in experimental and computerational.
By experimental methods, synthetic jet (a new phenomenon of acoustic streaming) was first found in 1988 and applied to control the flow about circular cylinders. A sheared wing tip was developed to improve performance of lift/drag ratio, to modify the China-made civil air plane Y-12. A swinging strake on the nose tip of the slander body at high angle of attack can efficiently diminish the asymmetric side forces. Wave cancelation method was used for active control of boundary layer transition from laminar to turbulent. Recently, a new technique, flow deflector, has been developed to increase the maximum lift coefficient by 25% and to delay the stall angle of attack by 5 degrees.
The mainly successful researches and appliations in computational research fields including both CFD and optimization are shown as follows:
- Meta-model assisted design optimization with application in aeronautics
- High-lift devices design optimization
- Multi-disciplinary optimization based on game strategies
- Uncertainty based multi-objective design optimization in aerodynamics
Specific contribution to MARS Project
NUAA will contribute to the project in the aspects of technical management (T1.1 and T1.4), experimental research (Task2 leader) and optimization(T4.1 and T4.2). Contribution to Task2 is to develop advanced surface measurement techniques: surface hot film and optical flow method; design wind tunnel models; conduct experiments on back-facing step flow; develop new devices; analyze the effect of the Reynolds stresses on separation control and drag reduction
NUAA contribution in WP4, mainly in task 4.1 and 4.2 is devoted to establish meta-model approximation for expensive function evaluation and design optimization. To select the devices for effective control of oscillating separated flow and effective prevention of separation or drag. NUAA will provide its knowledge and expertise on optimization to facilitate seeking the best design of flow control devices. Mesh-free methods have flexibility to distribute points in computational domain, thus the method can be extended to treat complex control devices. We may benefit to adjust only the region adjacent to the bodies due to using hybridized mesh/meshless method. Optimization of flow control devices using GAs or other methods will be implemented at NUAA with in-house developed solver of hybridized mesh/meshless method. In order to reduce the design cost, the procedure of optimization will coupled with reduced models (meta-model or POD). NUAA will provide its knowledge on design for seeking the best sets of design variables related to proposed flow control devices. Hybrid Nash Games; Hierarchical Stackelberg Games, Multi-objective Evolutionary Algorithms will be provided to the consortium.
|
THU
|
Situated on several former royal gardens of the Qing Dynasty, Tsinghua University was established in 1911 originally as a preparatory school for students supported by the government to study in universities in the United States. With a splendid legacy accumulated over the past 90 years, THU has retained its character and charm, becoming the national centre for training engineers and scientists with both professional proficiency and personal integrity. The university currently has over 1200 full professors and 1,100 associate professors, 27,000 students, including 13,800 undergraduates, 8,600 master's degrees candidates and 4,600 doctoral candidates.
The School of Aerospace Engineering, transformed from the Department of Engineering Mechanics in May 2004, has the strongest teaching and research capacity in fluid mechanics in China. According to the recent government disciplinary assessments, THU ranks first in fluid mechanics. The research efforts at THU with respect to aerodynamics and aeroacoustics include development of advanced numerical methods, adaptive grid technique and simulation and modelling of turbulent flows with DRSM, nonlinear EVM, LES, and RANS-LES hybrid method approaches.
THU’s contribution to MARS project will be carried out by the Laboratory of Advanced Simulation of Turbulence (LAST) in the School of Aerospace Engineering. LAST has 4 faculty members and about 16 fulltime postgraduate students. In recent years LAST has engaged in a number of international and domestic collaborations.
Specific skill related s to MARS
The base flowfields are predicted by solving Navier-Stokes equations. It provides a number of differencing convective schemes including Jameson-type central with artificial viscosity, Roe, van Leer and AUSM+, etc. and implicit LU-SGS dual-time marching to account for flow unsteadiness with MPI parallel computation. The unsteady turbulent flows are predicted by RANS/LES hybrid methods, such as eDDES, iDDES or SAS.
THU has investigated flows including vortex generators on the supercritical wing, before a cavity, in a diffuser. Also, the tiny configuration modifications on the afterbodies are also applied to reduce the base drag. THU had investigated a number of flows with flow control devices and gained some significant design experience.
Specific contribution to MARS project
THU will contribute on task 3.1 and 3.2. Our in-house code is of finite volume approach solving Navier-Stokes equations on arbitrary multi-block structured grids. A number of convective schemes and time stepping methods are available in the code. In the calculation of Reynolds stresses the original RANS/LES hybrid methods, such as DES and DDES, have been implemented in the code. The code has been successfully validated against a number of flows including separation flows, shock wave/boundary layer interaction and multi-components interaction.
In task 3.1, THU will develop advanced RANS/LES hybrid methods, such as extended-DDES or improved-DDES, to well predict the base flows around NACA0015. The innovative unsteady-RANS method, which is independent on grid scale, is plannd to be introduced and developed for the base flows. THU will develop new, efficient and memory-saved turbulence statistic analysis and Reynolds stress extraction methods.
In task 3.2, THU will numerically calculate the base flows around NACA0015 and explore the flow physics. At the same time, the computational results will be compared with the measurements to validate the numerical methods. THU will also investigate the flow control devices, such as stable vortex generators and plasma on the NACA0012 surface.
|
AVIC-FAI
|
The First Aircraft Institute of AVIC (FAI) is located in Yan liang district, Xi'an City, Shan xi province. It’s also called as Xi’an Aircraft Design institute. It is an institute focusing on transport aircraft design and specializing in configuration design and aerodynamic design.
Several milestones of China Aviation Industry History were set up by this institute, the first Chinese civil aircraft—Y7, the first China’s fighter-bomber—FBC-1, the first China’s business aircraft—LE500. Especially FBC-1, nicknamed “China’s Flying Leopard”, is the first successful independent aircraft development in China, which won the top prize of the National Scientific Progress Award in 1999.
Under the support of the government, FAI has finished the farther construction of its basic facilities and technical innovation. Today, there are more than 20 research divisions in the institute, such as aircraft configuration, aerodynamics, structure design, strength analysis, landing gear, avionics, flight control and hydraulic system, engine and fuel system, environmental control system, etc.
There are more than 2000 employees in the institute, including one academician of Academy of Chinese Engineering, several state-level experts, almost one thousand senior engineers. The institute was also authorized to issue master degree, and it is a doctor research station as well.
Having accumulated the experience of international cooperation project—MPC-75, AE-100 pre-development, FAI are facing the new opportunity, that is Advanced Regional Jet (ARJ21). They are confident of winning the success.
Specific skill related s to MARS
FAI has done a lot of research on flow controls on aircrafts. “micro vortex generator” project was carried on several years ago, software for the vortex simulation were developed; vortex effects were tested in wind tunnel.
|
AVIC-ACTRI
|
ACTRI was found in 1958, originally the Northwest Computing Institute of Chinese Academy of Science, and now belongs to China Aviation Industry Cooperation (AVIC). The institute is located in Xi'an, a very ancient city in central of China mainland. Historically, ACTRI was a national high performance computing center, and now the institute is mainly engaged in the development of airborne and missile-borne computers, and aeronautical software. Currently ACTRI owns 1,046 employees on the staff, and there are several research centers hosted by ACTRI, among which is the Aeronautical Laboratory of Computational Fluid Dynamics (ALCFD). ALCFD is established by AVIC in October 1995. It is the one and only professional CFD organization in China aviation industry. Currently there are 21 researchers specializing in CFD discipline. The laboratory means to be the bridge between academy and industry. From 1990 to 2000, ALCFD had acted as the coordinator of a persistent national project to develop an integrated software system for aerodynamics numerical simulations. Recently the research focus has been switched to verification and validation of CFD simulations, and aerodynamic database. ALCFD is active, notably hosted the 12th national CFD conference in 2004, and co-organized the first and second national CFD validation workshops in 2003 and 2005 respectively. ALCFD also acts as the deputy coordinators since 2005 of AEROCHINA and AEROCHINA2, the international cooperation projects between Europe and China.
Background information and experience
Experience in development and application of software platform for credible aerodynamic numerical simulations has been accumulated, and in-house CFD solvers for external aerodynamic design, both multi-block structured grid RANS solver and hybrid grid RANS solver, have been developed. Under the framework of Flow Control technologies, numerical researches on flowing mechanism for vortex generator (passive flow control), suction/blowing and synthetic jets (active flow control) have been broadly investigated, which emphasis is lying on the separation flow control, drag reduction as well as on the lift enhancement.
Specific contributions of ACTRI to the MARS project
The main contributions and interests of ACTRI on the MARS project are mainly put on the numerical simulation for flow control (WP3) that includes:
1) to develop advanced simulation tools for turbulence modeling with at least 2 capabilities among URANS, hybrid RANS/LES and LES;
2) to perform turbulence flow statistic analysis, in particular for apparent stress and Reynolds stress extraction;
3) to perform step flow and wing flow simulations with/without flow control devices (especially with emphasis on those devices with suction /blowing, or synthetic jets);
4) to study the scale effects (e.g., Re effect) on flow control devices.
Besides, we also have interests on the synthesis analysis from experimental and computational data to improve understanding effects of flow control on Reynolds stress.
|
NPU
|
NPU is situated in Xi'an, a world-famous ancient capital city. The president of NPU is appointed directly by the State Council. NPU is one of the 15 key universities in China, and the country's only multi-disciplinary university of science and technology featuring the engineering education of aeronautics, astronautics and marine engineering with the stress on engineering and with the integration of engineering, science, management and humanities. At present, there are nearly 20,000 students studying at the University including over 10,000 undergraduate and two-year college students, and over 5,900 master's and over 800 doctoral students. In the University, there are 3 state key subjects, 8 state key laboratories and specialized laboratories, and 9 provincial and ministerial key laboratories and engineering research centers. The University owns a low-speed aerofoil wind tunnel -the largest of its kind in Asia- and an unmanned light airplane research and production base -the largest of its kind in China.
Developed for aeronautic research and dedicated to the prosperity of China's aviation industries, the Aeronautic Academy was among the earliest established faculties of NPU, representing the characteristics of the university. Incessant endeavour in the last 48 years has transformed the Department into a highly significant research base handling key disciplinary subjects in China's aeronautical study. Currently the Department offers three major specialties: Aircraft Design, Fluid Dynamics, and Solid Mechanics, which respectively belong to three first-class disciplines of aerospace science and technology.
The research organizations directed by the Department of Fluid Dynamics include: National Key Aerofoil and Cascade Laboratory, Aerofoil Research Center, Research Center of Aerodynamics, and Shaanxi Turbofan and Pump Engineering Center. The faculty consists of 12 professors (including 7 doctoral advisers), 11 associate professors, and 6 senior engineers. Three of them are "Experts with Outstanding Contributions" of the nation or of the aeronautical sphere, or excellent scholars back from abroad, and two of them have been awarded the internationally renowned Alexander von Humboldt Fellowship. Now the Department owns the largest low-speed aerofoil wind tunnel and the largest compressed continuity high-speed aerofoil wind tunnel in Asia, the fully digital hydraulic-servo experiment system, high-speed computers capable of billion calculations per second, several high quality SGI and SUN workstations along with some other first-class experiment facilities of China.
Specific skill related to MARS for NPU
NPU has devoted to the boundary layer testing again since 2006. The low turbulence Wind Tunnel (LTWT) of NPU is the mostly used facility in this period. The 2D test sections size of LTWT is (width * height):400*1000(mm). The primary testing facilities for boundary layer experiment in this wind tunnel are hotwire system, 3-D traverse system, and PIV system.
The stability in 3-D boundary layer was the primary research item from 2006 to 2009, by using velocity profile scan with hotwire in the boundary layer both along the span-wise and normal-wise on a swept wing in the LTWT. 3-D traverse system was used to put the probe at the certain place in boundary layer and move the probe in small steps (the least step is 0.1mm) in three directions. The structure in boundary layer such as cross flow vortex can be displayed by present experiment. Moreover, the turbulence elements array was introduced to try to affect the stability of 3-D boundary layer.
The research work in NPU-LTWT contains:
- NPU have done some work about the flow structure measurement in boundary layer.
- The method to introduce the source of turbulence has been considered in NPU, and the reception of the boundary layer has been taken into account.
- The experiment techniques such as hotwire, PSD data processing are prepared for present study.
Also, NPU has done some other work related to MARS:
- Active flow control by using micro zero-mass-flux jet. Including the design of highly efficient actuator;active separation control on airfoils in wind tunnel;numerical simulation study.
- Leading edge roughness for transition Control on Swept Wings, wind tunnel experiment research by using hotwire and sublimation method.
- Vortex generators placed on the wing or flap to control the separation, studied by wind tunnel experiment and CFD.
- Separated flow control by using plasma actuators.
- Fluidic vector thrusting study by using numerical simulation methods
Specific contributions of NPU to the MARS project
The main contributions of NPU for MARS project are mainly on WP2 and WP4.
For WP2, Dr. LI and his workgroup will establish an experiment model in wind tunnel with the abilities to involve the passive or active control systems. Especially, NPU will devote to study the design and manufacture of the MEMs system to accomplish the passive or active control system, and the MEMs system used to flow-field measurements.
As the leader of WP4, Prof. Gao and her workgroup will investigate methods to establish optimization models and the system of aerodynamics optimization with its experience on optimization design for MDO. It will study robust design optimization methods for aerodynamic configurations and different kinds of surrogate model tools for expensive function evaluation (meta-model, POD, ROM, and so on).
|
PKU
|
Peking University is a comprehensive and national key university of China. The university has effectively combined research on important scientific subjects with the training of personnel with a high level of specialized knowledge and professional skill. It strives not only for improvements in teaching and research work, but also for the promotion of interaction and mutual promotion among various disciplines.
The College of Engineering was officially established. The College was designed to focus on future engineering science and new technology, and is able to promote interdisciplinary research using Peking University’s vast resources. The College currently has five departments and five research centers. In addition, the College runs the Stake Key Laboratory of Turbulence and Complex Systems (SKLTCS), an esteemed center for research and pioneering ideas.
Since the foundation, the College has made great strides in its scientific research and the funding increases four times. In 2008, the Funding approved was over 100 million RMB. In the past three years, The College successfully initiated 98 new national research projects, six international cooperation projects, 31 province projects and 176 cooperation projects with enterprises. Currently, the College of Engineering has 250 projects.
The SKLTCS was established under promotion and supporting by Prof. Chou Peiyuan, the famous scientist and the founder of turbulence modeling theory. SKLTCS focuses on providing new understanding of the nonlinear complex system, such as turbulence, life science and system science. The Lab makes the following threefold as its mission:
- To gain fundamental knowledge about the complex phenomenon through theoretical and experimental research;
- To develop new and improved model for the study of complex evolutionary process;
- To play the important role of an academic, theoretical and idea center at Peking University and moreover in the nation.
Background information and experience
Under WP2: Experimental Investigation Flow Control Mechanism
The members of CH6 under WP2 have long-time strong experience and deep physical insights on various shear-flow instability and receptivity, near-wall vorticity and vortex dynamics, and shear-flow controls by on-wall or near-wall devices. In particular, they have developed a unique set of theories and methodologies for pinpointing the underlying mechanisms of shear-flow controls based on high-accuracy experimental and numerical data. Also, they have been studying how the shape and distribution of on-wall roughness elements affect the boundary-layer stability, transition, and skin friction, and have started to make important new discovery. All these background experiences and theories will be directly applied to MARS Project and further developed during application.
Specific contribution to MARS Project
WP2: Experimental Investigation Flow Control Mechanism
- Fully utilize the output of both WP2 and WP3 to extract the key physics responsible for the most effective and efficient control strategy. The method of such a flow diagnosis is based on the local on-boundary fluid dynamics theory and linear/nonlinear stability and receptivity theory of near-wall flow structures. Special attention will be paid to the flow structures responsible for the periodic part of those Reynolds-stress components that dominate turbulent friction drag and boundary-layer separation.
- Conduct an independent fundamental research on the physical sources and basic control principles of different near-wall Reynolds-stress components that affect most strongly the turbulent drag and turbulent boundary-layer separation.
- Conduct an independent fundamental research on the possibility of passive control of turbulent drag and turbulent boundary-layer separation by specially designed and optimized wall roughness elements.
|
BUAA
|
Beihang University (formerly Beijing University of Aeronautics and Astronautics), BUAA in abbreviation, was founded on October 25, 1952. Located at the center of Zhongguancun Science Park, next to China' s National Olympic Center, in Beijing, BUAA is the China' s first university of aeronautical and astronautical engineering.
Since its founding, BUAA has been one of the key universities given priority for development. In the new century and millennium, BUAA was officially listed in China's Action Plan for the Revitalization of Education in the 21st Century. At present, the university comprises of 17 schools and 6 departments, covering such diverse fields in sciences, engineering, liberal arts, management, languages, etc. There are currently more than 3300 faculty and staff members, including 10 academicians of either the Chinese Academy of Sciences or the Chinese Academy of Engineering Sciences, and over 1400 full or associate professors. The total enrolment reaches over 26,000, including more than 1300 doctorate candidates, over 5000 master candidates, and about 300 overseas students.
Background information and experience
BUAA has evolved from an engineering institute of aeronautics and astronautics into an open, multi-disciplinary, research-oriented university of engineering sciences and technology, preserving at the same time with strong research capability on aerospace engineering. Currently, there are 42 research institutes or interdisciplinary research centers in BUAA, accompanying with 11 key disciplines of the national level, and 89 laboratories, including 4 national key laboratories, 5 national specialized laboratories, and 12 provincial- or ministerial-level key laboratories. In recent years, BUAA has ranked among the foremost in China in terms of funding for scientific research, and become one of the China's important bases for scientific and technological innovation and quality education for high-level personnel.
Specific skill related to MARS
Experimental study (from Prof. Liu Peiqing)
1) Numerical and experimental studies were conducted for suction-blowing drag-reduction control of a 2-D airfoil. It was found that at the same Reynolds number, compared with the leading-edge suction without blowing, the suction-blowing control results in a better drag reduction.
2)Active flow control of complicated vortices was investigated experimentally for delta wing.
Simulation (from Dr. Zhang Jinbai)
In the last two years, supported by Airbus, a numerical study on Micro-blowing technique (MBT) have been done in BUAA.
MBT is a new technology for reducing turbulent skin friction with very low energy consumption. The flow problem related to the MBT is highly complex. It involves flow structures composed of multi-scale interactions.
Parametric studies are performed for active MBT flow control to investigate the drag reduction mechanism in local flow field. The numerical results demonstrate, respectively, the influences of the blowing factor, porosity, the slenderness and diameter of the micro-channel to the drag reduction capability by the MBT. By comparing with the experimental results published by NASA Glenn Research Center, the same qualitative tendency on the influences of the above stated relevant parameters to the drag reduction can be achieved, although the results would appear some discrepancies quantitatively.
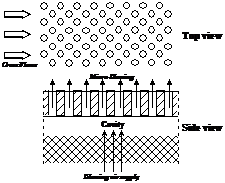
Specific contribution to MARS Project
In WP2, Prof. Liu Peiqing’s contribution has two components:
The first one is on the basis of fundamentals of the hot-wire technique to measure the Reynolds stress tensor. A kind of single hot wire probe will be designed and made.Explorations for the hot-wire probes used to measure Reynolds stress in theory and practical will be made. Factors affecting hot-wire measurements are considered. Reasonable one of measuring methods is picked up to finish the measurement.
The second one is on the design of impulse-blowing actuator and experimental system for NACA0015 flow control. The driving factors and configuration factors influencing characters of the impulse jet will be analyzed and summarized. Finally, a design criterion of impulse-blowing actuator for flow control is determined.
In WP3, Dr. Zhang Jinbai will perform numerical simulations for basic flow and validation with experimental data. The simulations will be based on URANS solver and LES solver. Furthermore, the influences of local micro-blowing on basic flow will be studied by means of numerical simulation. The interaction of basic flow and local micro-blowing flow will be analyzed to identify the flow control mechanisms affecting the skin friction and flow separation.
|
ZJU
|
Zhejiang University (ZJU) is one of the few top-rank research institutions of higher learning in China. It is a center of high-level teaching and research, where renowned academics from China and other countries work together contributing to the economic development and social progress of China and the world. At present, the total number of full-time students has reached over 39,000, including 22,900 undergraduates, 9,500 postgraduates working for master's degrees and 6,600 PhD candidates. Among its 8,400 faculty and staff members, there are over 1,200 full professors and 2,400 associate professors.
The School of Aeronautics and Astronautics (SAA) of Zhejiang University was established in 2007. The SAA mission is to promote development of the disciplines such as aeronautics, astronautics and mechanics, as well as to develop new areas within Zhejiang University. By aiming at national demands and grand challenges, the SAA is dedicated to be a prestigious research and education institution to train creative and interdisciplinary talents in the fields such as aeronautics and astronautics for China. Currently the number of faculty and staff members in the SAA has reached 74, of which 22 are professors, and 27 are associate professors. The SAA offers a full range of educational programs, including one undergraduate and nine postgraduate programs. The nine programs are: Flight Vehicle Design, Aerospace Propulsion Theory and Engineering, Navigation, Guidance and Control, Aerospace Information Technology, General and Fundamental Mechanics, Engineering Mechanics, Solid Mechanics, Fluid Mechanics, and Fluid Machinery and Engineering.
Center for Engineering and Scientific Computation (CESC), Zhejiang University, is a key interdisciplinary research center. The mission is to emphasize the nature of being interdisciplinary and multidisciplinary, and to promote applications of high performance computing in various fields in the university. It also provides high performance computing facilities for the university community.
Background information and experience
A problem solving environment, named the High End Digital Prototyping (HEDP) system, has been developed through the efforts of researchers in our group. The HEDP system was proposed to take advantages of continuously developing computational methods and computing resources, and to promote their practical engineering applications. It provides a unified, flexible and efficiency environment for large-scale multidisciplinary application simulations, such as structure analysis, fluid dynamics analysis, and thermal-hydrodynamic analysis. There are four categories of modules inside the HEDP system, i.e. the pre-processing module, the computing module, the post-processing module and the platform control module. The task parallel and data distributed computing schemes have been utilized in this system. Therefore, the HEDP equips users with an integrated platform including mesh generation, numerical libraries, visual steering and large-scale visualization capabilities.
Using the developed algorithms, programs and tools for the HEDP system, we have been successfully simulated the fluid flow, mixing and combustion. Figs. 1 and 2 show two representative simulation results obtained.
A parallel CFD solver has been developed to solve the full compressible Navier-Stokes and multi-species equations on hybrid grids with a kind of high-order Taylor-Galerkin schemes. The basic built-in algorithms and models are inherently of capability to treat with external flow problems, which have been extensively validated. The Large-Eddy Simulation technique was adopted in our solver to model turbulent flow separation from the surfaces of aircrafts. LES and DES are powerful numerical tools to study the complicated unsteady, turbulent phenomena. In the present project, we will implement the LES/DES method to resolve the flow field.
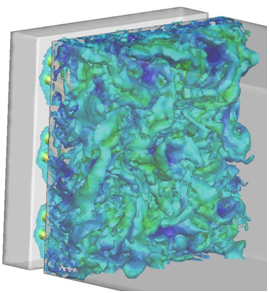
Flow separation from the upper surface of a wing.
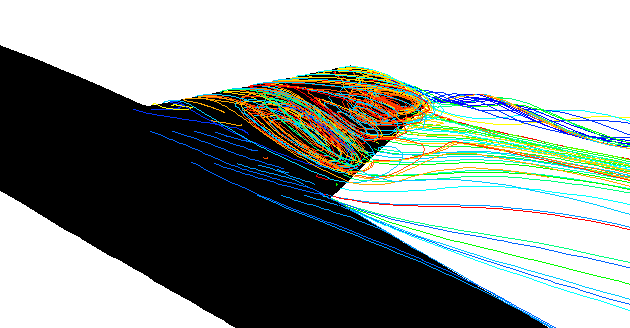
LES Result of Lean-Direct Injection Combustor with Discrete-Jet Swirlers.
Specific contribution to MARS Project
Our contributions to the present project are two-fold, i.e. Task 3.1 and Task 3.2 in WP3 for Numerical Simulation for Flow Control.
Active flow-control (AFC) is a fast growing multi-disciplinary science and technology thrust aimed at altering a natural flow state or development path into a more desired state (or path). Fig. 3, as an example, shows a schematic description of the spatial arrangement of intelligent structures for AFC. Based on our extensive work using the computational fluid dynamics package, we will develop a fluid-structure interaction code featured with moving mesh and Large-Eddy simulation techniques for the present project.
With the developed numerical tool, fundamental researches on the intelligent structure design and arrangement for the active flow-control will be performed, including the mechanisms of flow separation, lift/drag force production, and so on. Based on the simulation results and the Reynolds stress manipulation, we will carry out the selection of devices for effective control of oscillating separated flows.
|
|